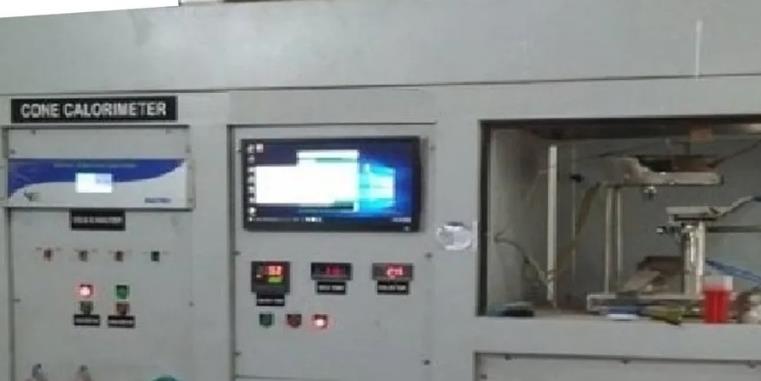
CONE CALORIMETER
What is it?
A cone calorimeter is a device used to measure the thermal behavior of small samples of materials in their condensed phase. Its extensive use is in fire safety engineering, where it is employed to study how different materials burn. The calorimeter can measure the heat release rate, smoke generation rate, ignition time, oxygen consumption status, carbon monoxide, carbon dioxide generation, and mass loss rate of the given material sample.
A cone calorimeter is a scientific instrument used to measure the heat release rate and smoke production of materials when they are exposed to an external heat source. This information is valuable for evaluating the fire performance of materials and products, and for developing fire safety standards and codes.
The cone calorimeter consists of a small, sealed chamber with a cone-shaped opening at the top. A sample of the material to be tested is placed in the chamber, and an external heat source is applied to the material through the cone-shaped opening. The heat release rate and smoke production of the material are measured using sensors within the chamber.
Heat release rate is a measure of the rate at which a material releases heat as it burns. It is typically expressed in kW/m2, and is an important factor in determining the fire hazard of a material. The higher the heat release rate, the more quickly a fire can spread and the more intense it will become.
Smoke production is another important factor in fire safety. Smoke can obscure visibility and make it difficult for people to escape a burning building. The smoke production of a material is typically measured in terms of the amount of smoke produced per unit area of the material, and is expressed in m2/m2.
Cone calorimeters are widely used in the construction, transportation, and aerospace industries to evaluate the fire performance of materials and products. They are also used by fire safety researchers to study the mechanisms of fire spread and to develop new fire safety technologies.
In addition to measuring heat release rate and smoke production, cone calorimeters can also be used to measure other fire performance characteristics, such as the ignition temperature of a material and the amount of toxic gases produced during combustion.
The use of cone calorimeters has greatly improved our understanding of the fire behavior of materials and has led to the development of more effective fire safety measures. For example, the results of cone calorimeter testing have been used to develop fire resistance ratings for building materials, which are used to evaluate the fire safety of buildings.
Cone calorimeter testing is typically conducted in accordance with standardized test methods, such as the ISO 5660 and ASTM E1354 standards. These standards specify the apparatus, heat source, and test conditions to be used in the testing of materials.
The results of cone calorimeter testing can be used to compare the fire performance of different materials and to predict the fire behavior of materials under different conditions. For example, the results of cone calorimeter testing can be used to compare the fire performance of different types of insulation materials or to predict the fire behavior of a material when it is used in a particular application, such as in the walls of a building or as a component of an aircraft.
The Principle of Cone Calorimeter
Numerous test procedures are available to assess a material's capacity to respond to fire, including the Small Flame Source Test (ISO 11925-2), the Oxygen Index (LOI) Test (ISO 4589-2, ASTM D2863), the Horizontal and Vertical Flammability Test (UL 94), and the NBS Smoke Density Test (ISO 5659-2, ASTM E662).
They generally include small-scale testing of a single material property, only evaluating its performance in a controlled environment. It cannot be used to predict how a material will behave in a big fire.
Many nations, areas, and international standards organizations have employed the cone calorimeter, one of the most effective fire test tools, to study the combustion characteristics of materials in construction materials, plastics, composite materials, wood products, and cables.
Heat Release
According to the concept of heat release, 13.1 MJ of heat is produced per kilogram of oxygen consumed, and the net heat of combustion is proportional to the amount of oxygen required for burning. The test involves:
- Burning samples under ambient air conditions.
- Detecting the oxygen contents and exhaust gas flow rates.
- Exposing them to an external irradiance between 0 and 100 kW/m2.
Smoke Release
The basis for measuring smoke is the law that states that light intensity decreases exponentially with distance when it passes through a volume of combustion products. The percentage of laser light intensity that passes via smoke in an outlet pipe is used to calculate smoke obscuration.
According to Bouguer's law, this proportion determines the extinction coefficient. In the test, samples are burned in ambient air while exposed to external irradiation ranging from 0 to 100 kW/m2, measuring smoke obscuration and emission gas flow rate.
Mass Loss
The test specimens are burnt above the weighing instrument while exposed to external irradiation between 0 and 100 kW/m2, and the mass loss rate is measured.
The Cone Calorimeter Applications
- Analysis of Material Combustion Properties
Analyze the combustion risks of various materials based on the results of the cone calorimeter test (e.g., HRR, Peak HRR, TTI, SPR, etc.) and choose the right ones to utilize for various applications.
- Study of Flame Retardant Devices
The structure of materials can be modified to produce materials with superior flame retardant qualities by repeated testing and test data comparison.
- Fire Model Study
Create several fire model types by looking at the heat release rate, smoke release rate from burning materials, trend analysis, or connecting to a medium-scale test model (ISO 9705).
Testing Procedure Of Cone Calorimeter:
All the devices which were used before the invention of this device were also known to be faulty, and they had many types of experimental errors. However, there were radical changes in the design that made the device's operation reliable. A cone calorimeter is considered one of the essential devices for fire protection engineering and fire testing. This device encases a sample in Aluminium foil, a retainer frame and wool. A conical heater is also placed for the materials to combust, and the heating element provides a radiant flux that turns electricity into heat. The heater of this instrument is also open in the centre and allows the combustion products to flow upwards.
The most important part of the device is ventilation. A small water supply is also essential to cool and regulate the heat in the device's system. The combustion products travel through the cone heater and the instrumented exhaust pipe. The values which are calculated are not limited to the mass-loss rate during the process of combustion and the total amount of heat which is released during the test.
Several smoke production in this device and the room fire test have been analyzed, and all the good correlations have also been obtained when the products are divided into two groups-
- The products with more than ten minutes to flashover in the room fire test.
- The products with less than ten minutes.
These are the two categories which correspond to the two heat output levels in the room fire test. They are taken as 100kW for the first ten minutes and 300kW up to 20 minutes. The average rate of smoke production and the total smoke production for the products with more than 10 minutes to flashover are the useful parameters for the prediction of smoke release in the fire test.
However, on the other hand, the products with less than ten minutes, no parameter seems to be give any type of useful prediction.
It is a known fact that the products which release large amount of smoke tend to have a short time to flashover in the fire test. Hence, in this case, one should consider the smoke production in a classification system.
Properties that can be measured directly include:
- Heat release rate
- Ignition time
- Critical ignition flux
- Smoke production rate
- Optimum heat of combustion temperature
- Toxin emission rates
Advantages Of A Cone Calorimeter
A cone calorimeter is a valuable tool for evaluating the flammability of materials because it allows researchers to control and standardise the test conditions, such as the sample size, the fuel type, and the airflow rate. This allows for comparing the fire performance of different materials under the same conditions, which is essential for understanding the relative flammability of other materials.
There are several other advantages to using a cone calorimeter to evaluate the flammability of materials:
- Controlled Test Conditions: The cone calorimeter allows for the standardisation of test conditions, such as the sample size, the type of fuel, and the airflow rate. This allows for comparing the fire performance of different materials under the same conditions.
- Reliable And Repeatable Results: The cone calorimeter provides reliable and repeatable results, as the test conditions can be carefully controlled and the measurements are made using calibrated equipment.
- Wide Range Of Applications: The cone calorimeter can be used to test a wide range of materials, including plastics, textiles, and construction materials, making it a versatile tool for evaluating the fire performance of different products and materials.
- Efficient Testing: The cone calorimeter allows for the rapid evaluation of the fire performance of materials, making it a time-efficient tool for researchers and manufacturers.
- Cost-effective: The cone calorimeter is a relatively cost-effective method for evaluating the flammability of materials, especially when compared to large-scale fire testing.
- Comprehensive Evaluation: The cone calorimeter measures a wide range of fire performance parameters, including heat release rate, smoke production rate, and mass loss rate, providing a comprehensive evaluation of the fire performance of a material.
Limitations of a Cone Calorimeter
One of the main limitations of a cone calorimeter is that it is designed to replicate a small, controlled fire in a laboratory setting. This means that the results of a cone calorimeter test may not always accurately reflect the behaviour of a material or product in a real-world fire situation.
There are many factors that can affect the behaviour of a material in a fire, including the size and intensity of the fire, the presence of other materials or objects, and the ventilation and air flow in the environment. These factors are difficult to replicate in a laboratory setting, which can make it challenging to accurately predict the fire behaviour of a material or product.
Another limitation of a cone calorimeter is that it is limited in its ability to replicate certain types of fires. For example, it may not be able to accurately replicate a fire that is fueled by a liquid or a fire that is spreading over a large area. Additionally, the results of a cone calorimeter test can be affected by operator error, such as incorrect placement of the sample or incorrect calibration of the equipment.
Services Of Cone Calorimeter:
- Determination of HRR: The heat release rate is a pointer in determining the fire hazard of a material. The higher the HRR, the more flammable and explosive the material is, and the greater the danger of a fire. The cone calorimeter can measure the gas flow and oxygen accumulation, and calculate the heat release per unit of time and surface area. This information helps to calculate the HRR. This rate develops as a function of time and is typically used to analyze the fire properties of a material.
- Making Safety Regulations: This device is essential for an unhazardous environment while working with potentially combustible materials. Knowing the reaction of these materials can help to create safety regulations easily.
Summing It Up
Cone Calorimeters are vital testing equipment for many reasons. Not only do they help evaluate the fire performance of materials, but they can also provide important data on smoke generation and toxicity.
When choosing a cone calorimeter, it is crucial to consider the desired applications and objectives. With so many different models and features available on the market today, there is sure to be a cone calorimeter that meets your specific needs.
- For more details contact us:
- Website: https://kdmglobal.business.site
- Email : saleskdmglobal@gmail.com
- Website : https://sites.google.com/view/kdmglobal/home
- Contact :8218470498
Leave a Reply
Related Products
You Might Like Also
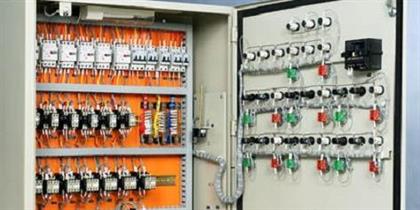
Power Control Panel
AMF Control Panel,Capacitor Panels,DG Synchronized Panel,Electrical Panel,HT Panel,Load Management Panel,Low Tension Panel,LT Control Panel,Main LT Panel,Motor Control Center Panel,Outdoor Power Panel,Power Control Panel,Power,Process Control Panel Distribution Panel,Synchronizing Panel,VFD Panel Read More
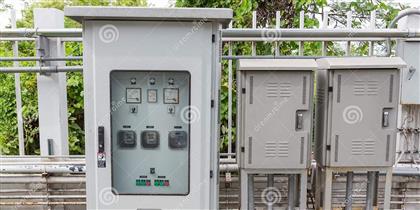
Outdoor Power Panel
AMF Control Panel,Capacitor Panels,DG Synchronized Panel,Electrical Panel,HT Panel,Load Management Panel,Low Tension Panel,LT Control Panel,Main LT Panel,Motor Control Center Panel,Outdoor Power Panel,Power Control Panel,Power,Process Control Panel Distribution Panel,Synchronizing Panel,VFD Panel Read More
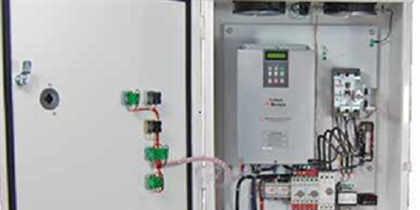
VFD Panel
AMF Control Panel,Capacitor Panels,DG Synchronized Panel,Electrical Panel,HT Panel,Load Management Panel,Low Tension Panel,LT Control Panel,Main LT Panel,Motor Control Center Panel,Outdoor Power Panel,Power Control Panel,Power,Process Control Panel Distribution Panel,Synchronizing Panel,VFD Panel Read More
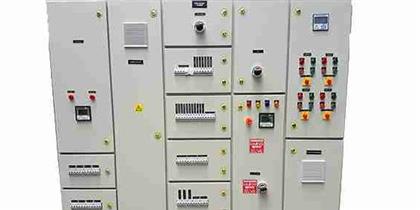
Power Destribution Panel
AMF Control Panel,Capacitor Panels,DG Synchronized Panel,Electrical Panel,HT Panel,Load Management Panel,Low Tension Panel,LT Control Panel,Main LT Panel,Motor Control Center Panel,Outdoor Power Panel,Power Control Panel,Power,Process Control Panel Distribution Panel,Synchronizing Panel,VFD Panel Read More
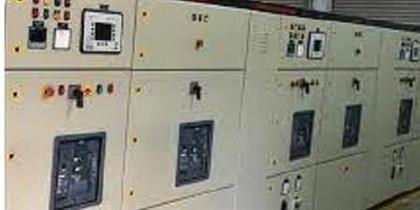
Synchronizing Panel
AMF Control Panel,Capacitor Panels,DG Synchronized Panel,Electrical Panel,HT Panel,Load Management Panel,Low Tension Panel,LT Control Panel,Main LT Panel,Motor Control Center Panel,Outdoor Power Panel,Power Control Panel,Power,Process Control Panel Distribution Panel,Synchronizing Panel,VFD Panel Read More
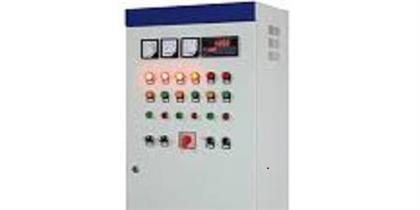
Process Control Panel
AMF Control Panel,Capacitor Panels,DG Synchronized Panel,Electrical Panel,HT Panel,Load Management Panel,Low Tension Panel,LT Control Panel,Main LT Panel,Motor Control Center Panel,Outdoor Power Panel,Power Control Panel,Power,Process Control Panel Distribution Panel,Synchronizing Panel,VFD Panel Read More
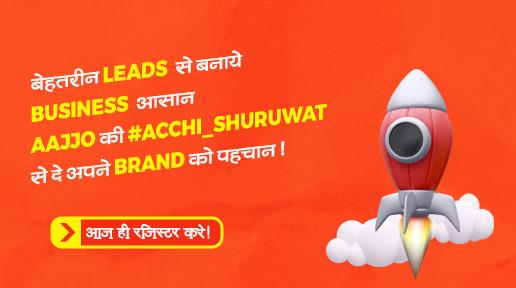
Comments
I hope that this project can bring a lot of benefits