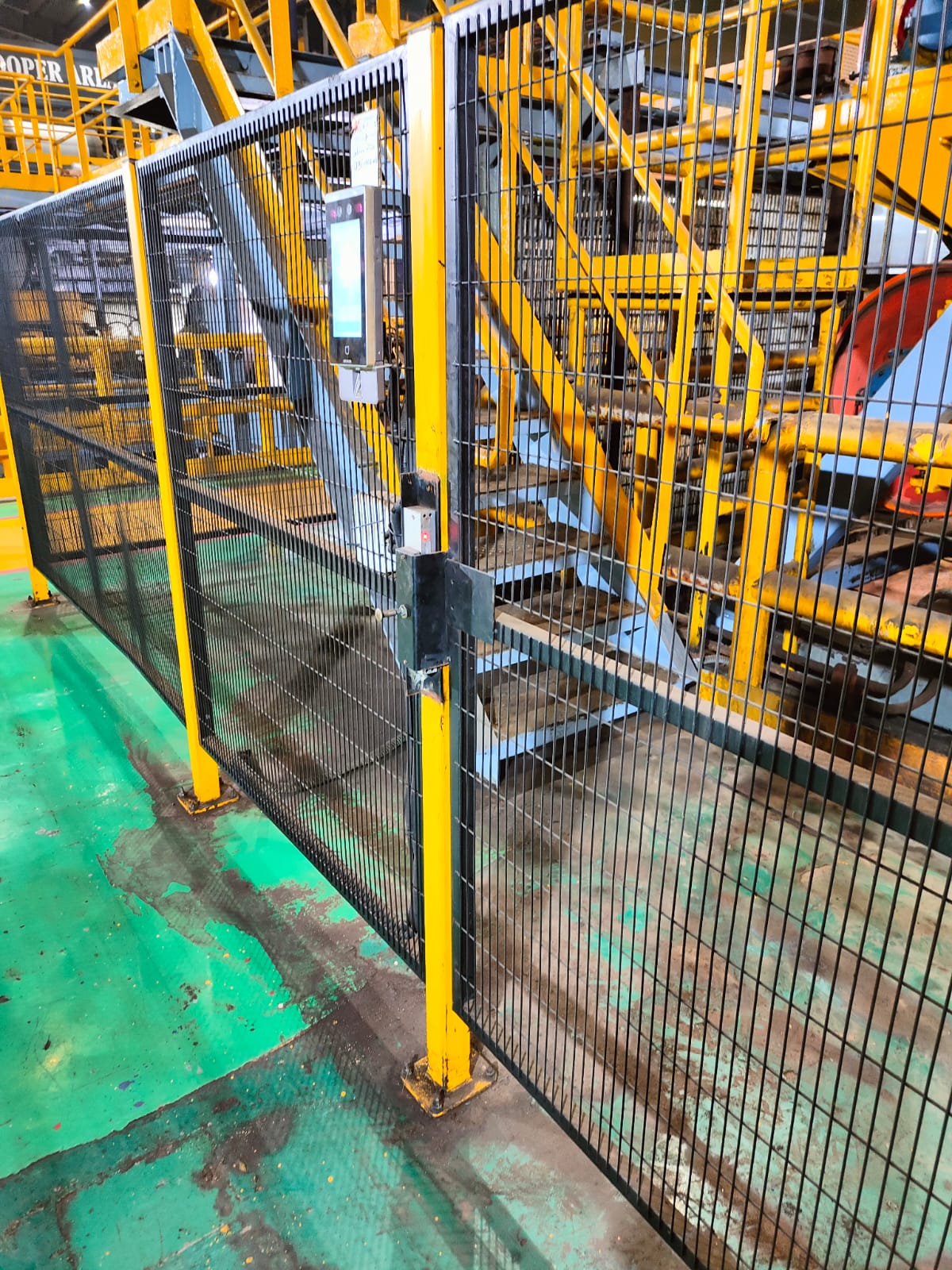
A safety fence in an industrial setting serves the crucial purpose of protecting workers from potential hazards associated with machinery, equipment, or specific areas within a facility. Here's a breakdown of considerations for an industrial safety fence:
Material Selection: Safety fences in industrial settings are often made from durable materials such as steel, aluminum, or reinforced plastic. The choice of material depends on factors such as the level of protection required, environmental conditions, and the type of hazards present.
Height and Strength: Industrial safety fences are typically designed to be tall and robust enough to deter unauthorized access and withstand potential impacts. The height and strength of the fence should be sufficient to prevent workers from climbing over or breaking through it.
Visibility: Safety fences should be highly visible to ensure that workers can easily identify the boundaries of restricted areas. This can be achieved through bright colors, reflective strips, or the use of warning signs and markings.
Access Points: While safety fences restrict access to hazardous areas, they should incorporate access points such as gates or doors for authorized personnel to enter and exit when necessary. These access points should be equipped with safety features such as interlocks or self-closing mechanisms to prevent accidental entry.
Customization: Industrial safety fences can be customized to suit the specific requirements of different environments. This may include features such as angled or curved sections to accommodate the layout of machinery or adjustable components to adapt to changes in workflow.
Regulatory Compliance: Safety fences in industrial settings must comply with relevant safety standards and regulations, which may vary depending on the industry and location. These regulations often stipulate requirements for fence height, strength, access control, and visibility.
Integration with Safety Systems: Industrial safety fences are often integrated with other safety systems such as emergency stop buttons, alarm systems, and safety sensors to provide comprehensive protection against accidents. These systems can automatically stop machinery or alert workers in the event of a safety breach.
Maintenance and Inspection: Regular maintenance and inspection of industrial safety fences are essential to ensure their effectiveness and compliance with safety standards. This includes checking for damage, corrosion, or wear, and repairing or replacing components as needed.
Leave a Reply
You Might Like Also
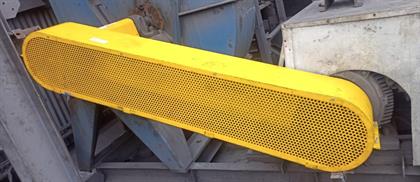
chain belt drive guard

pump coupling safety guard
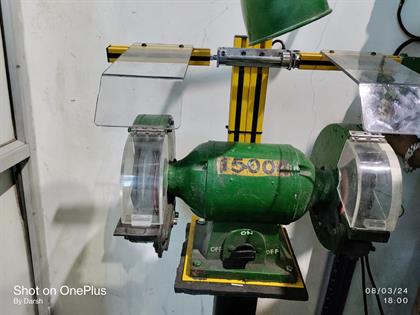
bench grinder machine safety guard
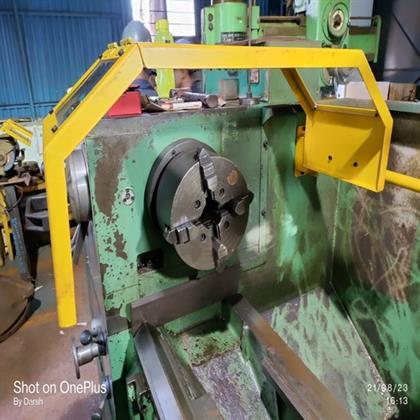
Lathe machine safety guard
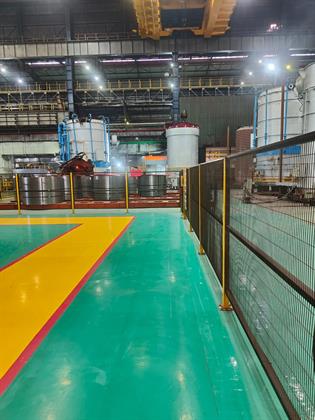
safety guards
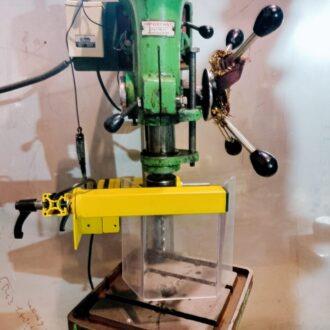